Sustainability Initiatives
Meridian Display has done “the right thing” for years, but until recently did not think of using this to differentiate ourselves. Now we have outlined and quantified some of the steps we have taken to conserve our resources.
The following is a list of just some of our daily practices, annual efforts, and one-time changes:
Daily Practices
We recycle 100% of our scrap with our baler. This adds up to 100,000 pounds of material being recycled per month.
We refurbish 30,000 pallets per month, and take the unusable boards off and chip them, which turns them into bedding for horses.
Our ink kitchen allows us to blend just the amount that we need, eliminating the need for extra ink to be ordered. Any extra ink is reblended into black or another color we can use.
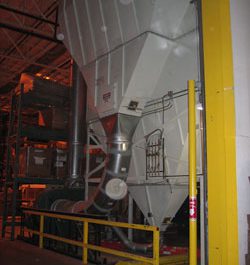
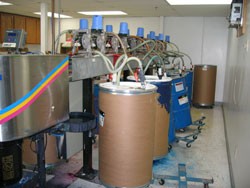
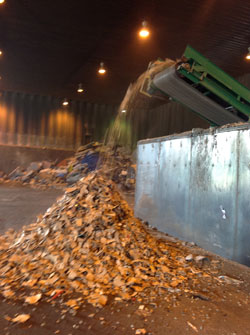
Annual Efforts
We are on Excel Energy’s summer program to be shut down during peak usage times. On hot days during the summer we switch the plant hours so we can finish production by noon to avoid using power during the heat of the day.
We do annual “Energy Audits.” With the first and second audits we condensed the number of air compressors we use from six to one more efficient unit with backups. We also sealed the lines and removed two pieces of equipment. In addition we replaced motors to more energy efficient models.
Annually we bring in a dumpster, and clean out our obsolete dies. They are taken to a special recovery facility that separates the metal from the wood and rubber portion of the dies. Our last load diverted 4.09 Tons from landfills. 15.75% of the load yielded metal for recycling. The remaining 84.25% of the load was wood, rubber and plastic that was shredded for burning to produce energy.
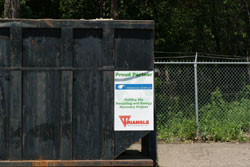
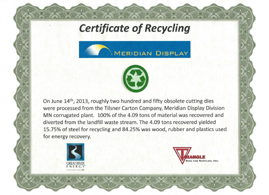
One Time Changes
We replaced our T12 light bulbs with T8 bulbs giving us a savings of 28,416 kilowatts per year, which amounts to a dollar savings of $2,280 per year.
We have replaced high bay florescent lights with T8 6 lamp fixtures. Each fixture reduces the wattage used from 460 to 220, which gives an annual savings of $51.00 per year per fixture switched.
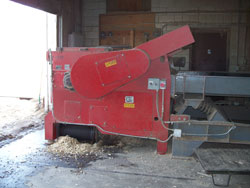
We replaced our gas powered forklifts with electric forklifts eliminating emissions in the plant, and decreasing our use of natural resources. The new forklifts have an auto-off system that is seat activated to conserve power, and the AC power system includes energy recovery provided by three forms of regenerative braking. They also have AC drive motors transversely mounted on the same axis, providing less mechanical energy loss and higher transmission efficiency.
We upgraded the power in our Pallet Division from old 208 to efficient 480 which required new switchgear, transformers and a capacitor.
We installed high-speed overhead doors in our pallet division to reduce the amount of time doors were open when forklifts went in and out.
We also shred and recycle office paper, collect cans and plastic bottles, and take them to a recycling center.